The Rare Air of the Semiconductor Fab
Microelectronics fabrication plants (fabs) are complex structures that require sophisticated air circulation and control. For management and energy savings, most of the conditioned air inside a fab is recirculated and may carry increasing amounts of contaminants that are produced internally, from humans, materials, chemicals, and equipment. About 5 – 20% of fresh air is provided from outside the fab, which may carry other potential contaminants. Small particles have been a well-controlled concern for decades, but modern microelectronics technology also requires a tight control of gas-phase, airborne molecular contamination (AMC) as it affects product, processes, and equipment. It is no longer possible to manufacture advanced semiconductors without AMC protection.
AMC is typically classified based on SEMI standard F021-00-1016. As technology nodes progress, contaminant sensitivities rise and are a greater influence on wafer yield.
AMC Sources
Internal and external sources of contamination contribute through outgassing of organic species, bases, and acids.
The History of AMC Filtration
Entegris' Jürgen Lobert walks us through the long history of AMC (airborne molecular contamination) filters and the adaptations of materials, technology, and people to find the purity needed in every aspect of our lives.
Featured Technical Paper
Fire Emissions and Smoke Impact on Industrial Environments
Smoke emissions from vegetation fires can have a significantly harmful impact on sensitive industrial processes and personnel health or wellbeing, both through particulate but also gas-phase component. Implementing AMC filters in air handlers and industrial environments can reduce the costly impact, protect processes and personnel, and increase production yield.
Featured Brochure
BrochureA detailed overview of AMC sources and trends, and recommended filtration solutions including our portfolio of VaporSorb™ Advantage filters.
AMC Trends
Today's fabs are manufacturing in cleaner environments as advanced processes are more AMC sensitive and there is a greater awareness of AMC impact. Early AMC concerns focused on few molecules only, at the ppm level. Over time, and particularly with 193 nm technology, more and more chemicals cause concerns, and with the advent of 14 to 7 nm critical dimensions, most gas-phase compounds can be a concern in certain process steps.
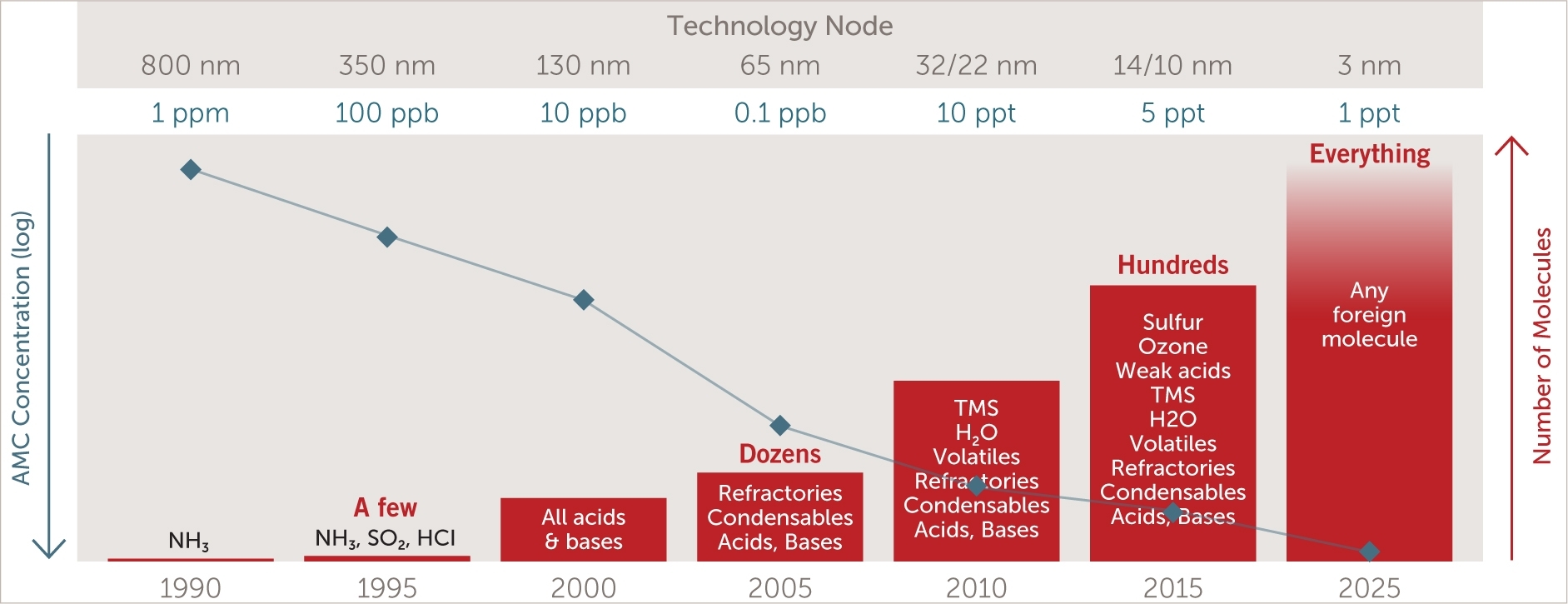
AMC Applications
Given the number of internal and external AMC sources, semiconductor processing now requires a multilayer approach to contamination control. A typical fab employs AMC filters at the ambient air inlet (make-up air handler, MUA), often in the recirculation or return air handlers (RAH) and on top of cleanroom ceiling fan filter units (FFU). Lithography tools have used AMC filters since the introduction of DUV technology 25 years ago. For advanced processes below 28 nm, however, there are increasing requirements for non-lithography tool protection. Sub-fab and plenum spaces below and above cleanrooms are not yet filtered in most fabs but may be AMC controlled in the future.
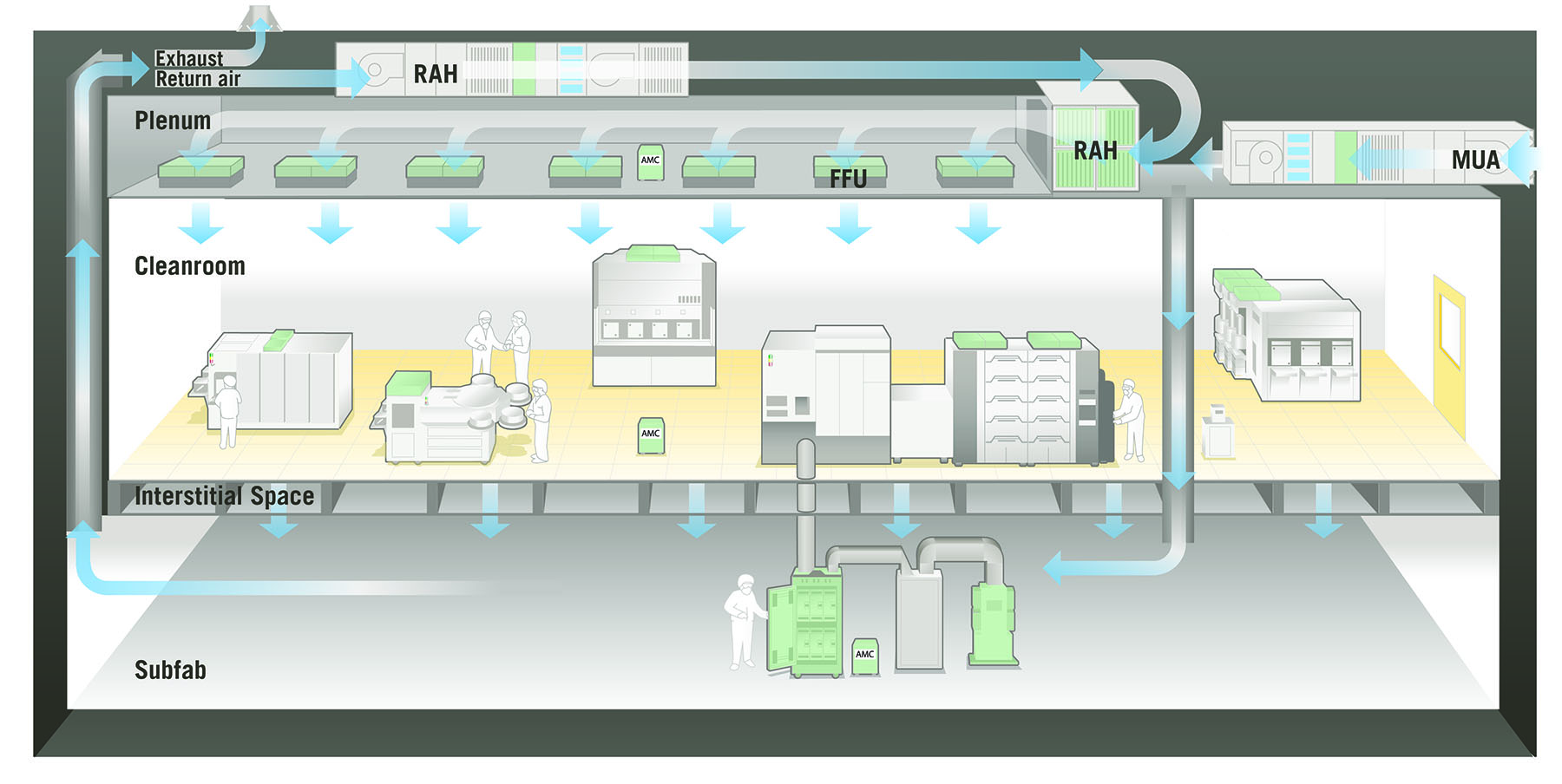
Application Notes
Interested in Airborne Molecular Contamination (AMC) Solutions for the Microelectronics Industry
Interested in Airborne Molecular Contamination (AMC) Solutions for the Microelectronics Industry
Interested in Airborne Molecular Contamination (AMC) Solutions for the Microelectronics Industry
Product Solutions
The AMC trends we observe in the industry are reflected in the needs of AMC filter solutions. Common AMC requirements and standard Entegris filtration solutions are tabulated below. Through the “See it. Control It.” program, specific contaminant removal blends are created based on data collected and analyzed by the Entegris Analytical Services labs globally.
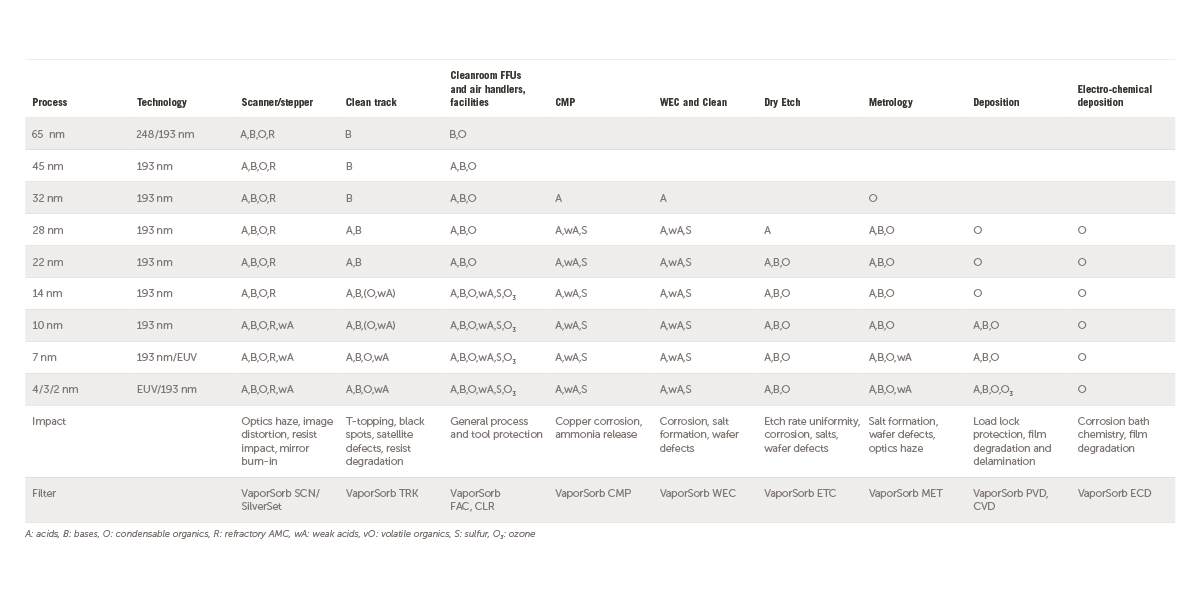
Entegris’ stepper and scanner filters are designed to provide reliable protection from airborne molecular contamination sources such as acids, amines, condensable organics. Use Entegris filters confidently in a variety of work areas and tool makers.
Tool-top and EFEM filtration solutions that deliver superior protection against the full range of airborne molecular contaminant in all non-litho applications including CMP, WEC, Dry Etch, and Metrology.
Superior protection for advanced semiconductor manufacturing environments at sub-65 nm modes. Field- and lab-proven for use in semiconductor manufacturing environments, including lithography, etch, CPM, metrology, and reticle storage areas.
Chemically purify environmental air used in photolithography exposure tools to protect optics and resists. These filters housing protect exposure tools from a full range of airborne molecular contaminants.
The SB300 front opening shipping box (FOSB) secures wafers during shipment and protects against contamination, vibration, and shock events. Our FOSB is the first to be FIMS compatible and has molded-in wafer supports that set it apart from the competition with precise and permanent wafer plane positioning for the entire life of the FOSB.
Our Spectra front opening unified pod (FOUP) holds 300 mm wafers safely and securely while they are being transported and transferred into thousands of sophisticated process steps. These FOUPs provide superior microenvironment control, optimum automation integration, and low cost of ownership.